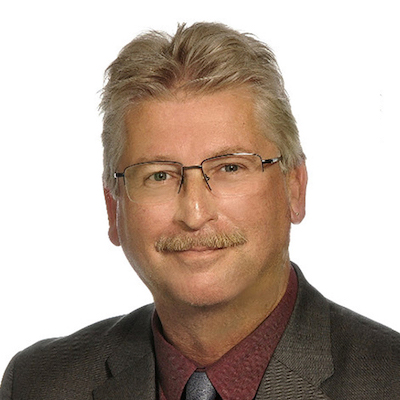
CBRE industrial advisory senior director Peter Millesse. (Courtesy CBRE)
Industrial has been the hottest commercial real estate asset class through the pandemic and a May 6 webinar presented by Urban Land Institute’s Toronto chapter explored how the sector is changing.
CBRE industrial advisory senior director Peter Millesse opened the proceedings by presenting an overview of industrial space demand and how the design and utilization of that space is meeting the needs of a new class of tenants.
CBRE industrial and logistics vice-president Samantha Sukumar then moderated a panel, asking questions of Broccolini development manager Andrew Sgro, Prologis VP and investment officer Robert Frost, and SCI senior director of procurement and contracts Jeff Seaman.
The webinar ended with all of the above taking viewer questions curated by Michael Linton, an engineer and associate with C.F. Crozier & Associates Inc.
Increasing industrial space demand
The explosive Canadian growth of e-commerce and support industries such as personal delivery and packaging supply companies has fuelled an insatiable thirst for warehousing and logistics space.
Millesse said for every $1 billion in e-commerce spending there is a corresponding requirement for 1.25 million square feet of distribution space. Continuing that trend through 2025 shows an industrial space requirement of more than 42 million additional square feet.
“As consumer demand increases and available technology improves, many distributors must increase their product delivery options in order to keep up with consumer expectations,” said Millesse. “The omni-channel consumer experience means that anyone can order anything at any time on any number of different platforms with any number of different delivery options.
“This flexibility in demand possibilities in turn requires more and more distribution space for increased inventory levels and multiple modes of fulfillment activities.
“So. this drive for industrial space and its specific needs has in turn fuelled innovation and many facets of industrial development, including facility design, location, construction techniques and even fulfillment and distribution-specific automation.”
Changing industrial buildings and properties
Demand for higher clear heights has been increasing because it enables greater vertical storage capacity through the use of racking and mezzanine levels. Millesse said new industrial facilities in the Greater Toronto Area (GTA) are approaching a norm of about 40 feet.
Wider spacing between building columns is allowing for greater flexibility for an occupier’s rack configurations and minimizing column interference.
Warehouse lighting systems and increased light levels are advancing the increased use of bar-coded labels and computer screens which require increased visual acuity.
“High-efficiency LED lighting with motion sensors are now used to increase light levels and minimize operating hours,” said Millesse. “Natural light supplementing through the use of skylights and sidelights is also increasing, resulting in improved employee well-being.”
Millesse said a greater awareness of employee retention, safety and diversity has led to increased requirements for related employee amenities, such as gym and workout areas, recreational areas, prayer and meditation rooms, and increased security provisions such as permanent on-site staffing and emergency assistance stations.
“Many distributors are pushing for more urban-centred last-mile distribution points to be as close as possible to their customer base,” said Millesse. “Some are achieving this through the development or redevelopment of existing sites, close to the centre of heavily populated areas.
“Others are achieving this through the conversion of existing unused urban-centric retail space to order fulfillment space. Many have also developed a hybrid model, reducing the amount of in-store shopping area of their urban outlets and replacing it with product fulfillment areas for online order pick-up.”
Environmentally sustainable trends such as the use of timber framing and green or living roofing systems, common in some West Coast markets, are also emerging in Ontario. So are the development of multi-storey facilities and the use of prefabricated modular components.
Truck-level door counts are increasing on a per-square-foot basis, allowing for greater flexibility for occupiers’ receiving and shipping functions, increased efficiency and shorter trailer turnover times.
Trailer parking and secure yard provisions are becoming more common, allowing greater occupier flexibility and scheduling of shipping and receiving activity. It also allows for the use of drop trailer programs to minimize downtime for drivers.
Increasing reliance on technology
Millesse said artificial intelligence is being used for on-site design optimization and to enhance planning and scheduling, while 3D printing technology replicates required components on-site that previously had to be constructed elsewhere and then shipped.
That’s just the tip of the technological iceberg.
“The use of photovoltaic glazing can produce enough electricity to make a facility partially self-reliant for power,” said Millesse. “Even the use of drones for building inspections and completion status updates is becoming more and more prevalent now.”
Innovations within industrial facilities to streamline the fulfillment and delivery process, such as the use of robotic systems, are saving time and increasing order accuracy.
Changing supply chain model
While the just-in-time model can help improve profits by limiting inventories to save on costs, the pandemic has shown weak links in the supply chain can cause slowdowns or breakdowns. That can lead to shortages of critical goods.
Sukumar — who works with both landlords and tenants across the GTA on sales, leasing and investment on existing space and new product — asked the panelists if they see the just-in-time model changing.
“I don’t see any of our clients or any of our businesses moving away from a just-in-time model,” said Seaman, whose company SCI is a Toronto-based third-party logistics provider. “I just don’t think the costs of real estate allow people to stockpile mass amounts of inventory.”
Prologis is the largest global owner of industrial warehousing with close to a billion square feet, and Frost is responsible for growing the portfolio in the GTA.
He didn’t see a sudden surge of stockpiling during the pandemic, but he’s heard discussion about it. He thinks there will be a bit of a shift from exclusively just-in-time to just-in-case models and holding more inventory.
Omni-channel delivery
Frost said omni-channel has changed the way people are doing business and setting up their supply chains. The process involves moving goods both in bulk to retail outlets and individually to consumers to create a seamless and fast-moving consumer experience.
It also needs to account for reverse logistics due to product returns.
Seaman said SCI is looking more closely at the end consumer and investing in more technology and automation in an attempt to make “pick, pack and ship” operations more efficient.
Broccolini specializes in industrial and residential development. Sgro said it’s looking at including a retail component in new industrial buildings as consumers have become more comfortable with picking up goods they’ve purchased at non-traditional locations in addition to stores and malls.
Raising the bar on clear heights
Fifteen million square feet of new industrial development is expected in the GTA next year, according to Sukumar, who added some owner-users are building up to 90-foot clear heights.
Building industrial facilities to such heights is very complex and technical. Sgro said when you start to move into larger buildings with specialized uses, questions arise about utilities, power and water availability, and the number of employees needed.
Millesse said anything above a 50-foot clear would typically be constructed specifically for a client’s particular uses and not be built on spec.
Seaman said automation is needed to take advantage of 90-foot clear height buildings. He noted Tim Hortons and Walmart have been successful in reducing their footprints by building higher and implementing that automation. A premium also needs to be placed on safety training as you go higher, Seaman added.
“I do think you’re going to continue to see clear heights edge up,” said Frost. “We’re planning 42-foot clear on a couple of our developments over the next couple of years.
“I know we’re in the middle of building a 50-foot clear spec building in California right now.”
Multi-storey industrial buildings are common in Asia and have recently been built in Seattle, New York City and Chicago.
With the GTA’s high land prices, Frost believes it’s just a matter of time before multi-storey industrial arrives. He doesn’t think it makes financial sense in other Canadian markets, owing to the high cost to build and the rent needed to justify it, and thinks multi-storey would only be built for specific users – not on spec.
“Over the next 12 to 24 months, what I think you’ll see is an end-user come into a design-build. And maybe it’s not three storeys of warehouse, but maybe it’s warehouse on the ground floor and then you got a couple storeys of van parking or something like that.”
Industrial expansion in the GTA
Distribution and logistics facilities have historically been concentrated in the western GTA, but as expansion options there dry up, the boundaries of what’s considered the core GTA industrial market is expanding north and east into Durham region.
“I don’t think tenants have the luxury any more of just saying ‘I want to be in Mississauga or Brampton and ‘I want 300,000 square feet in Q4,’ ” said Sukumar, who noted construction location decisions are often made based on when a user needs a building.
Frost said buying entitled industrial land in the GTA is “obscenely difficult.”
“You think you can bring a site on in 12 to 24 months, and it turns out it’s 48 months. And that’s why you’re seeing, in an 800-million-square-foot market, a one per cent vacancy rate. We just can’t build the product fast enough to keep up with the demand.
“You’ve got the Greenbelt to the north, you’ve got the lake to the south and that’s why you’re seeing markets like Durham and Hamilton starting to pick up steam for tenants that don’t have a lot of options.”
Sgro said once a company makes a decision on being in the western or eastern part of the GTA, it typically stays in that market. The east has gained appeal because there’s more land available and it’s generally less expensive, though that’s changing.
“We’re starting to look at a lot of redevelopment, where developers are coming in and taking down obsolete product in order to build something that’s considered more first-class and can offer higher cubic capacity for the reason that we can’t find ready-to-go land in the core GTA market anymore,” said Sukumar.