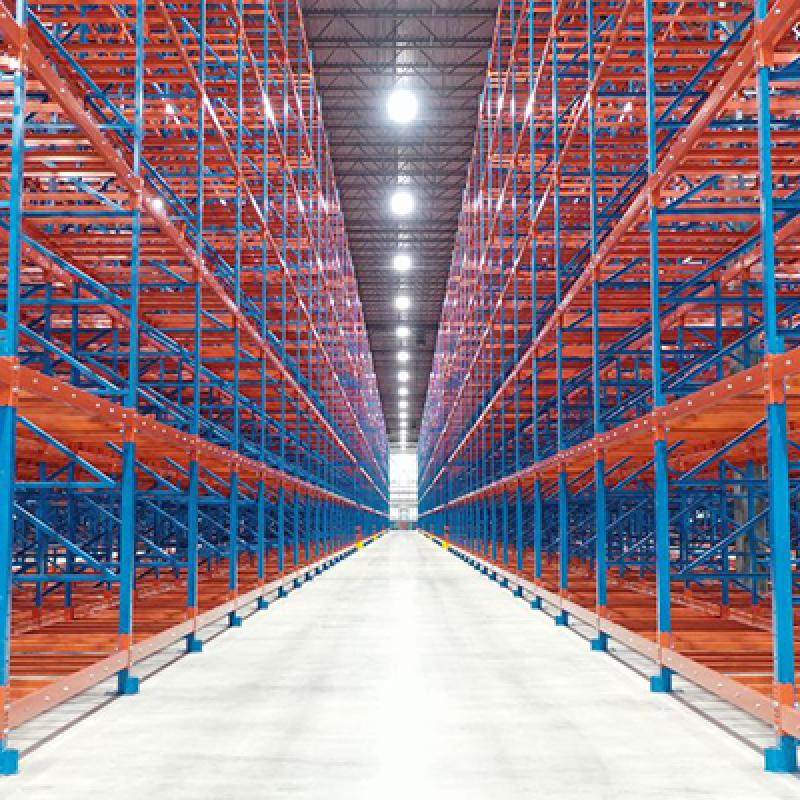
The floor slab of an industrial building might not seem like the most exciting topic, but it’s one of the most critical factors influencing the efficiency and safety of pallet racking systems.
Whether you’re an industrial tenant or a real estate agent, understanding the interplay between floor slabs and racking systems can significantly impact operational success and leasing potential.
Why floor slabs matter in industrial spaces
Floor slabs form the literal foundation of any industrial operation. For businesses reliant on pallet racking systems, the slab’s quality and specifications directly influence racking performance and safety. The following factors underscore the importance of floor slabs:
Load-bearing capacity: Pallet racking systems can exert significant point loads on the floor. A slab’s load-bearing capacity must align with the weight of goods stored and the design of the racking system.
Flatness and levelness: Uneven or sloped slabs can destabilize racking systems, increasing the risk of collapse. In high-bay warehouses, even minor imperfections can lead to significant operational issues.
Durability and longevity: Cracked or deteriorating slabs compromise safety and necessitate costly repairs or reinforcements.
Seismic considerations: In seismic zones, the slab must accommodate additional anchoring and bracing requirements to meet building codes and ensure safety.
The impact on industrial tenants
For industrial tenants, a well-constructed floor slab ensures smoother operations, reduced downtime, and enhanced safety. Here’s how:
Safety assurance: Properly leveled and load-rated slabs prevent tipping or shifting of racking systems, safeguarding employees and inventory.
Cost efficiency: Avoiding slab damage minimizes repair costs and prolongs the lifespan of both the floor and the racking system.
Operational efficiency: Smooth slabs improve forklift maneuverability, reducing wear on equipment and enhancing picking accuracy.
Before signing a lease, tenants should verify that the slab’s specifications align with their intended racking design and storage requirements. Conducting a pre-lease inspection with a racking expert can save significant headaches down the line.
Why industrial agents should care
Real estate agents often focus on location, square footage, and ceiling height when marketing industrial properties. However, overlooking the quality of the floor slab can result in dissatisfied tenants and underperforming properties.
Informed marketing: Highlighting a property’s floor slab specifications—such as load capacity and flatness—can appeal to prospective tenants with heavy storage needs.
Avoiding liability: Ensuring that the floor meets code requirements and is suitable for industrial racking systems can protect agents from potential legal issues.
Tenant retention: Properties with robust floor slabs attract high-quality tenants and foster long-term leases, reducing turnover rates.
Engineering insights: Technical considerations for floor slabs
From an engineering perspective, several factors influence the relationship between floor slabs and pallet racking:
Reinforcement and thickness: Slabs should be engineered with the appropriate thickness and reinforcement—typically rebar or mesh—to handle concentrated loads.
Control joints: Properly placed control joints mitigate cracking and help maintain the slab’s structural integrity.
Surface treatments: Epoxy coatings or sealants can enhance durability and reduce wear, particularly in high-traffic areas.
Anchoring systems: Pallet racking requires secure anchoring to the slab. The slab’s composition and condition dictate the type and depth of anchors used.
Best practices for industrial stakeholders
Whether you’re an industrial tenant, agent, or facility manager, the following practices ensure optimal outcomes:
Collaborate early: Engage a racking expert during the design or leasing phase to evaluate slab suitability and recommend necessary adjustments.
Regular maintenance: Routine inspections of the slab and racking system can identify and address issues before they escalate.
Future-proofing: Anticipate potential operational changes, such as heavier loads or taller racking, and ensure the slab can accommodate these needs.
Partner with experts
Navigating the complexities of floor slabs and pallet racking doesn’t have to be daunting. At North American Steel, we specialize in designing, engineering, manufacturing, and installing racking systems that align with your building’s specifications. Our experts can assess your facility, recommend solutions, and ensure your operations run smoothly and safely.
Have questions about your floor slab’s compatibility with pallet racking? Contact us today to speak with one of our specialists!