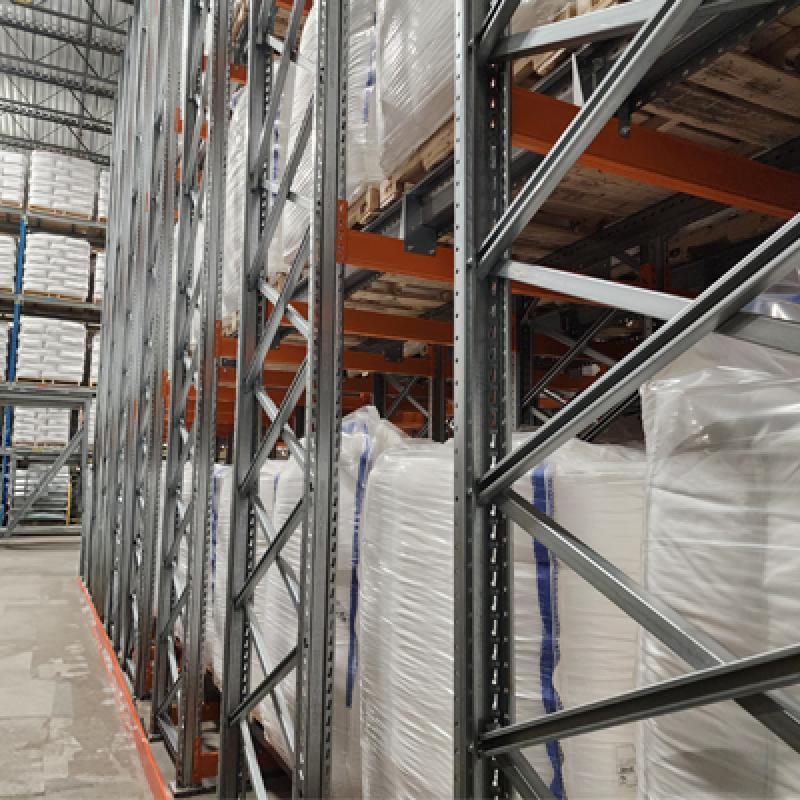
In the fast-paced realm of industrial real estate, efficiency is the name of the game.
As consumer demand surges, supply chains evolve, and real estate costs remain high, the pressure on businesses to optimise their storage and distribution operations intensifies. For industrial clients, the decision to transition to semi-automated or fully-automated storage systems, such as pallet shuttle carts, can be a strategic move towards enhanced productivity, competitiveness and long-term operating cost efficiencies. However, this transition requires careful consideration and collaboration with a trusted racking manufacturer equipped with a competent internal engineering department. Let's delve into when and why industrial clients should make this transition, examples of some of the types of industries that benefit, and the pivotal role of expert design and implementation.
The need for automation:
In today's industrial landscape, time is money, and every cubic foot of warehouse space counts. Traditional storage methods, while functional, may fall short in meeting the escalating demands for speed, accuracy, and scalability. This is where automated storage systems shine. By leveraging technologies like pallet shuttles, businesses can significantly increase storage density and inventory throughput, streamline operations, and minimise labour costs.
When to consider automation:
The decision to adopt automated storage solutions is not one-size-fits-all. Industrial clients should evaluate several key factors before making the leap:
Volume and velocity of inventory: As inventory levels rise and order fulfilment demands surge, manual handling becomes increasingly inefficient. A sudden spike in demand or the need to accommodate seasonal fluctuations may signal the right time to transition to automation.
Space constraints: Limited warehouse space for palletized products can hinder expansion and compromise operational efficiency. Automated storage systems optimise vertical space utilisation while also allowing for unprecedented storage density, allowing businesses to maximise storage capacity without the need for costly facility expansions.
Labour challenges: The labour market volatility and rising wage costs underscore the importance of reducing reliance on manual labour. Automated storage systems minimise the need for human intervention in routine tasks, mitigating the risks associated with labour shortages and turnover.
Operational efficiency goals: Businesses aiming to enhance throughput, accuracy, and order fulfilment speed stand to benefit greatly from automation. By eliminating manual errors and streamlining processes, automated storage systems bolster operational efficiency and customer satisfaction.
Industries benefiting from pallet shuttle systems:
Several industries stand to reap substantial benefits from the adoption of pallet shuttle systems:
Manufacturing: In the manufacturing sector, where efficiency and precision are paramount, automated pallet retrieval systems, such as pallet shuttles, streamline material handling processes. Manufacturers can optimise inventory storage, reduce downtime, and enhance production line efficiency by automating the retrieval of raw materials, components, and finished goods.
Distribution and logistics: Distribution centres and logistics hubs face immense pressure to meet ever-increasing demand while minimising operational costs. Automated and semi-automated pallet retrieval systems empower these facilities to efficiently manage inbound and outbound palletized loads, improve order fulfilment accuracy, and expedite shipping and receiving processes.
Cold storage and pharmaceuticals: Industries that require strict temperature control, such as cold storage facilities and pharmaceutical warehouses, benefit from the reliability and consistency offered by automated pallet retrieval systems. These systems ensure precise handling of temperature-sensitive goods, minimise the risk of product damage, and uphold compliance with regulatory standards.
Wholesale and retail: Wholesale distributors and retailers dealing with bulk merchandise rely on efficient storage and retrieval processes to meet customer demands. Automated pallet shuttle systems enable these businesses to maximise warehouse space utilisation, expedite replenishment cycles, and optimise inventory turnover rates, thereby improving overall operational efficiency.
Construction and building materials: The construction industry often grapples with the challenge of managing large volumes of heavy and bulky materials. Pallet shuttle systems provide construction companies and building material suppliers with a streamlined solution for storing and accessing palletized loads of lumber, steel, concrete, and other construction essentials, ultimately accelerating project timelines and reducing labour costs.
Engineering requirements and the role of racking manufacturers:
Automated storage systems impose stringent engineering requirements on racking structures to ensure compatibility with automation components, such as pallet shuttles and carts. Working with a racking manufacturer that can engineer a system to meet these requirements is crucial for industrial clients. These requirements include:
Structural integrity: Automated storage systems exert significant loads on racking structures during operation. Racking manufacturers must design systems capable of withstanding these loads while maintaining structural integrity and stability. Pallet shuttles and carts also operate on rails integrated within a racking structure. It is integral that the rails and racking components are engineered to work seamlessly in conjunction with each other.
Compatibility with automation components: Pallet shuttle systems rely on precise coordination between racking structures and automation components such as shuttle vehicles and conveyors. Racking manufacturers must engineer systems that seamlessly integrate with these components to ensure smooth operation and optimal performance.
Customization and flexibility: Every warehouse has unique layout constraints and operational requirements. Racking manufacturers with internal engineering departments can design customised solutions tailored to the specific needs of industrial clients, providing flexibility and scalability for future growth.
In conclusion, the adoption of semi-automated or fully-automated storage systems presents a compelling opportunity for industrial clients to enhance efficiency, productivity, reduce operational costs and improve their competitiveness in their respective industries. By carefully assessing their operational needs, collaborating with a trusted racking manufacturer, and embracing cutting-edge automation technologies, businesses can future-proof their warehouses and unlock new levels of success in the dynamic industrial landscape.
If you are interested in learning about implementing an automated or semi-automated storage system into your facility, click here to reach out to our team of experts at North American Steel.